Oxyfuel creates a chemical reaction between the oxygen and steel that is so hot (about 1,800°F) the metal softens, and then melts
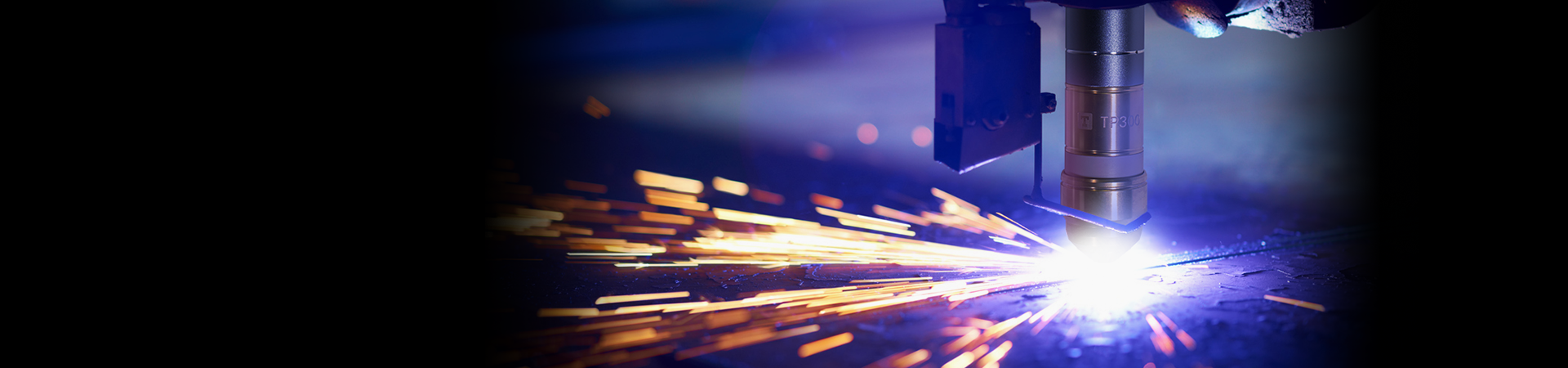
- BASIC KNOWLEDGE
- CHARACTERISTIC
- COMPAIRATION
- CUT QUALITY
- PRODUCTIVITY
- OPERATING COST
- Contact
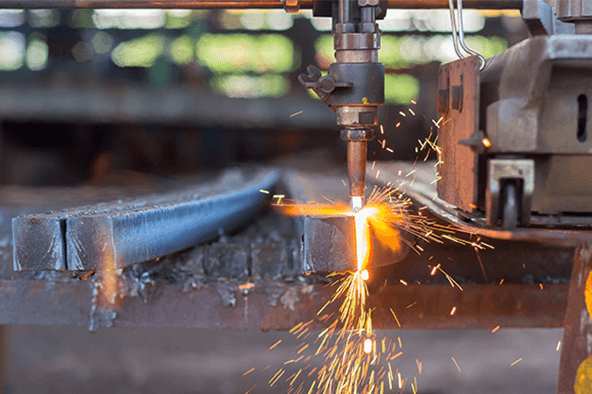
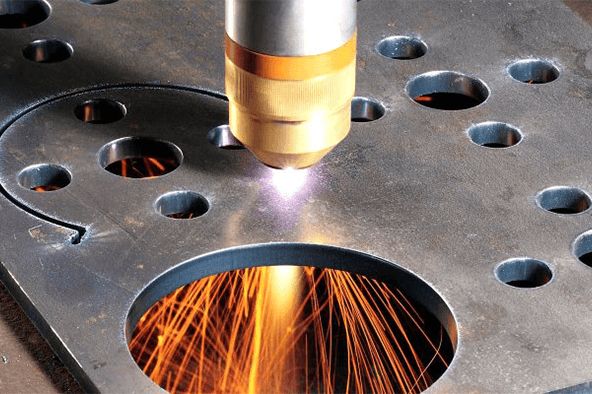
Plasma uses a high temperature ionized gas to produce a very hot, high energy-density arc that can cut any conductive material
Oxyfuel creates a chemical reaction between the oxygen and steel that is so hot (about 1,800°F) the metal softens, and then melts
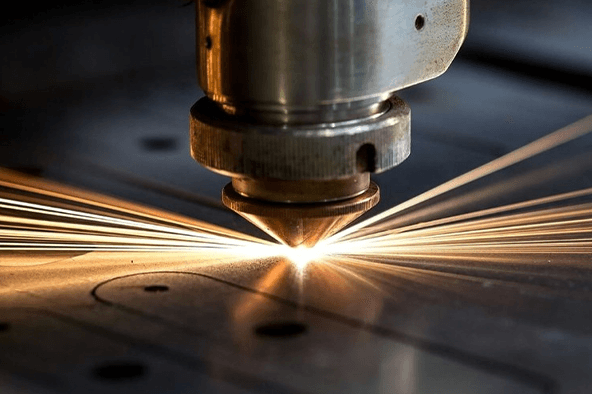
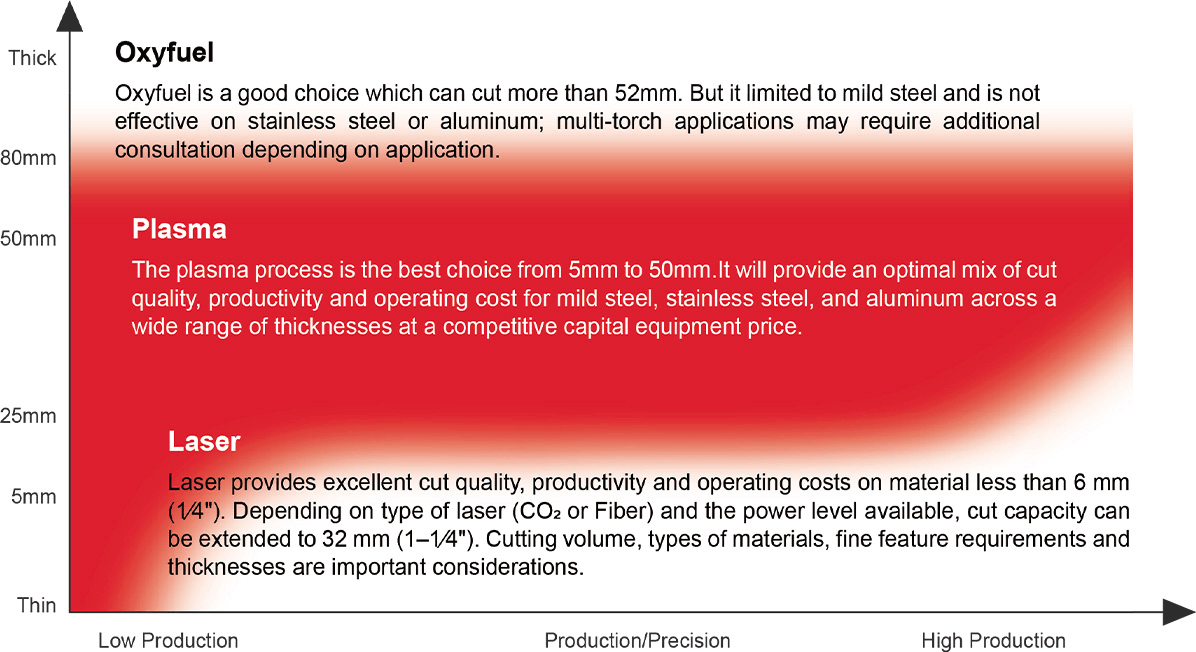
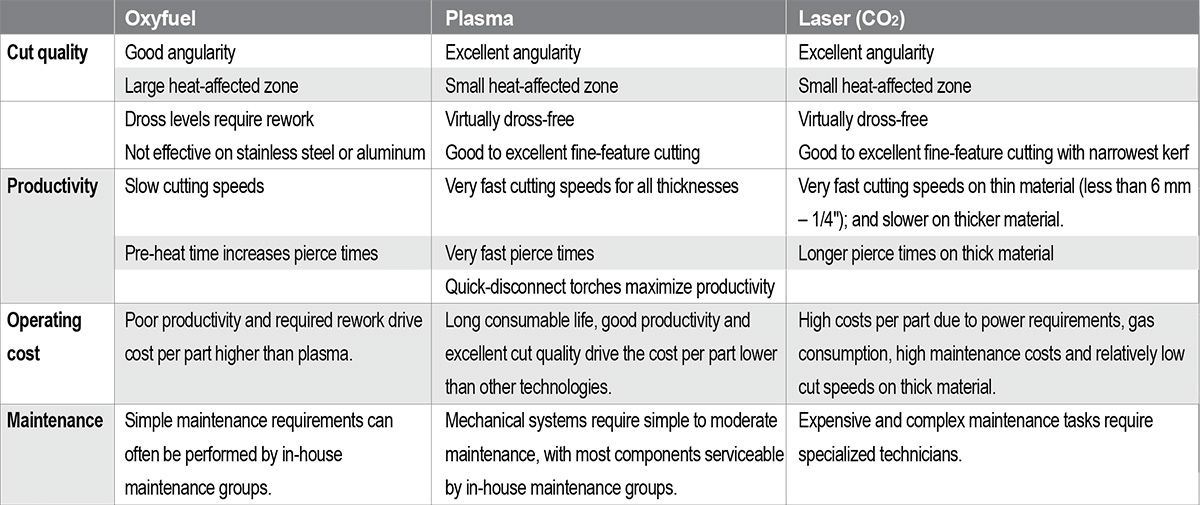
Different cutting applications require different levels of cut quality. This might be important because the cut edge will be visible to the buyer of the finished part or product. In other cases, cut quality matters due to its impact on downstream processes, such as welding or painting; weld-ready cuts will reduce the need for weld preparation, streamlining production and reducing labor costs. There are also times when cut quality is of lesser importance, and operators may opt to trade cut quality for higher throughput.
Cut quality is determined by a number of factors including:
· The motion of the cutting machine
· Whether the power level of machine is well-matched to the thickness of the material being cut
· What gases (or in the case of waterjet, abrasives) are being used
· Whether the machine settings and cutting consumables are properly matched
With some processes, especially oxyfuel cutting, the skill of the operator may be the most significant variable in determining cut quality. Other processes do not rely nearly as much on operator skill.
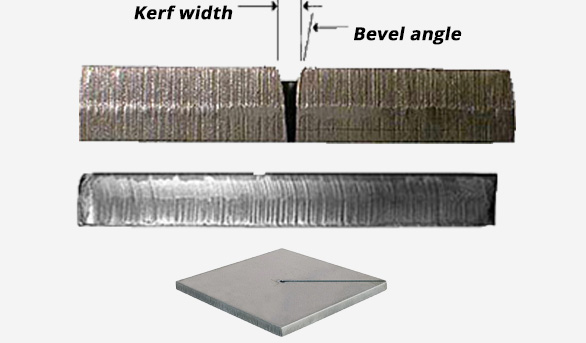
The quality of a cut is assessed according to the following properties:
· Angularity – a cut with little to no angle is considered best
· Kerf or width − a smaller kerf width enables finer part detail
· Tolerance – tighter tolerances mean a more precise, repeatable cut
· Size of the heat affected zone − a smaller zone protects the integrity of the metal better and impacts the viability of other processes such as welding and tapping
· Dross – less is generally better (dross is metal that melts during the cutting process and remains attached to the edges of the cut)
· Edge quality − smoothness of the finish
· Torch height control (THC) performance
Productivity is often incorrectly equated only with cut speed. While important, there are also other factors to consider. For example:
· Amount of programming time required
· Time required for job set up on the cutting machine
· Time required to prepare (or preheat) the system for cutting
· Number of cutting heads the machine can accept
· Efficiency of the nesting software and its ability to maximize cutting time and reduce unnecessary cutting head motion
· Ability to safely unload parts while the system is cutting
· Ability to perform multiple processes all on one machine – for example, cutting contours, cutting interior slots and holes, and beveling
· Integration of systems to perform parallel tasks such as preflow during traverse or IHS can improve process time
· Time required for secondary operations such as grinding, which may be reduced or eliminated by improving the quality of parts coming off the cutting machine
Many factors can impact the overall cost of operating a cutting system: consumables, power, gas, maintenance, etc.
Labor cost
Labor cost is also an important contributor to operating cost in most parts of the world; rising labor rates and the lack of skilled labor continues to drive demand for automated cutting solutions. To further improve operational costs, consider a fully automated solution that can reduce or eliminate:
· the need for programming and setup at the CNC
· secondary operations such as grinding for weld preparation
· the need for more than one machine to perform multiple process operations such as cutting, marking and beveling
Material utilization
Material utilization is another important contributor to operating cost. While in many cases it is possible to recoup some cost by selling unused or scrap material, it is far more beneficial to increase the utilization of that material so that there is less waste in the first place. A variety of factors contribute to material utilization; most notably, the CAD software that determines the part nest and directs the cutting motion.
When calculating operating cost, it is important to steer away from calculating just the cost per hour and instead focus on the cost per part or the cost per foot. Why? A system that costs ~$17.96 EUR ($20) per hour to operate but only produces two parts per hour is not nearly as efficient as one that costs ~$17.96 EUR ($20) per hour but produces 100 parts.
Cost per part = Operating cost per hour / number of parts produced
Cost per foot = Operating cost per hour / number of feet cut
Total cost
An even deeper assessment of operating cost requires understanding the total cost to produce a completed part, including downstream processes to prepare the part for welding or painting, or simply finishing the part for aesthetic purposes. When downstream processes – and the machine time and labor costs they require – can be reduced via improvements to the cutting process, total cost per completed part may be reduced.
One area often overlooked in a cutting system is Torch Height Control (THC) performance. A high-performance height control has the ability for automated process setup through the CNC or the Part Program to:
· reduce or elimate common setup errors
· compensate for electrode wear to maximize consumable life
· maintain proper height for optimal cut angularity
· detect torch collisions protecting the torch from damage